Revolutionary Hydrogen Generation
The Future of Clean Energy Storage
Hydrogien has developed a breakthrough hydrogen generation technology that fundamentally changes how the world can access clean energy. Our patented platform generates pure hydrogen on-demand from safe, solid-state materials and water – eliminating the need for dangerous high-pressure storage or complex infrastructure.
Key Advantages:
- Generate hydrogen anywhere, anytime
- No high-pressure tanks or pipelines required
- Works with any water source
- Operates in extreme environments
- Instant startup and shutdown capability
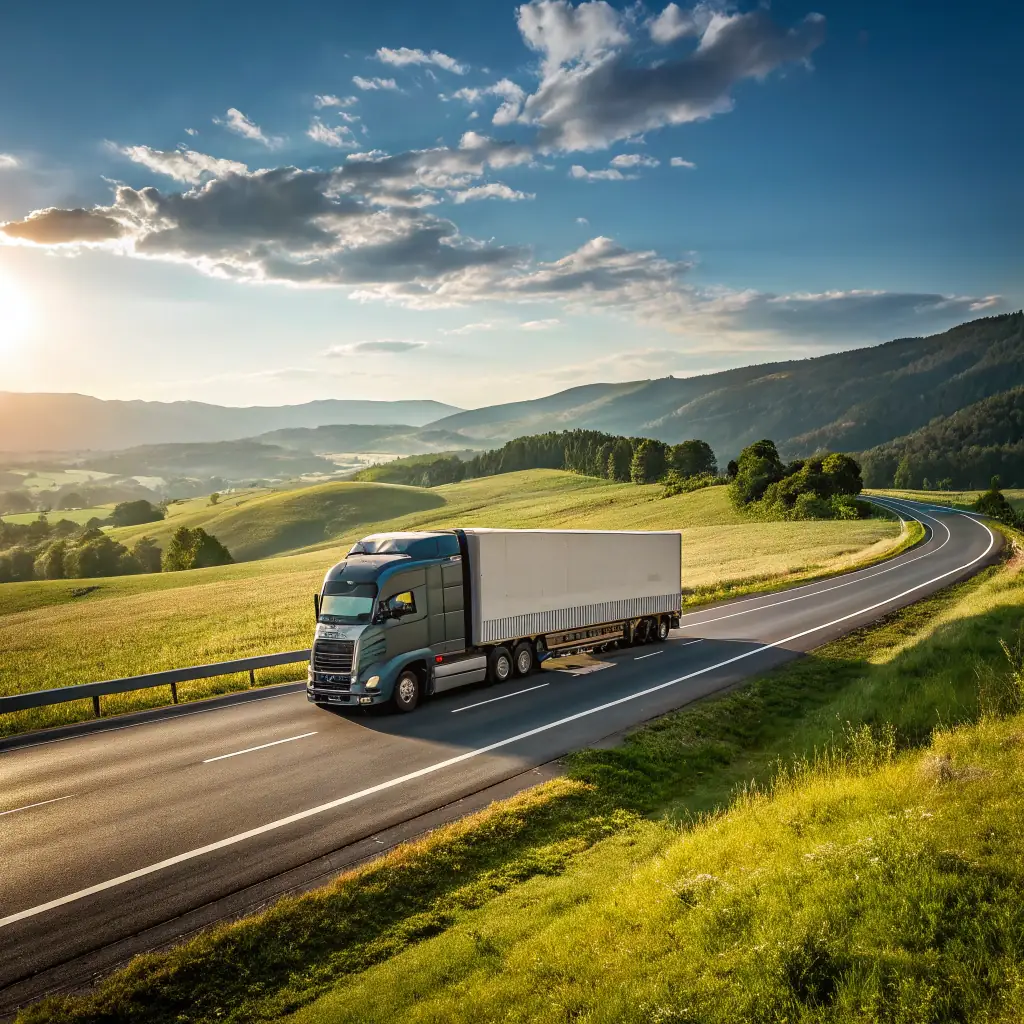
Unmatched Safety Architecture Setting New Standards for Hydrogen Safety
Our multi-layered safety system represents a quantum leap in hydrogen technology, with redundant protection systems that make our platform safer than conventional batteries.
Safety Features:
- Advanced predictive control systems
- Rapid emergency response capabilities
- Multiple independent safety layers
- Comprehensive containment systems
- Real-time monitoring and protection
Cost-Effective Production
Performance Metrics
Proven results with a 25-35% reduction in fuel consumption.
Deployment Success
Seamless transition from concept to reality, ready for integration.
Economic Advantages
Significant total cost of ownership benefits for your fleet.
Future-Ready Technology
Built to meet tomorrow's challenges with cutting-edge innovation.
Customer Support Excellence
Partnership beyond purchase, ensuring your success with Hydrogien.
Our Proven Results and Deployment Success in Hydrogen Technology
At Hydrogien, we pride ourselves on delivering tangible results. Our on-demand hydrogen generation system has demonstrated significant fuel consumption reduction and emissions lowering in real-world applications. We ensure a smooth transition from concept to reality, providing comprehensive support throughout the deployment process, ensuring customer satisfaction and environmental benefits.
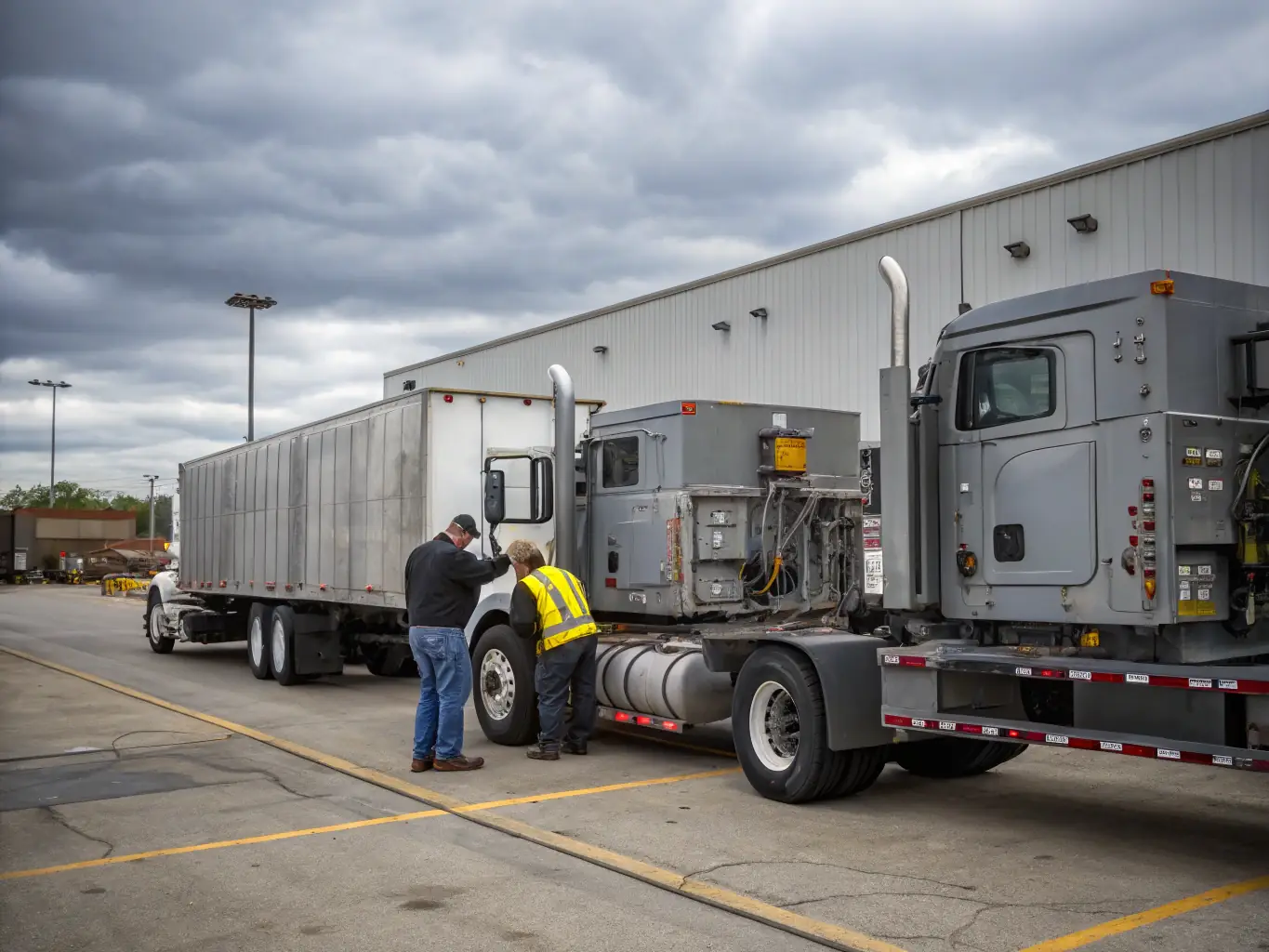
Seamless System Integration
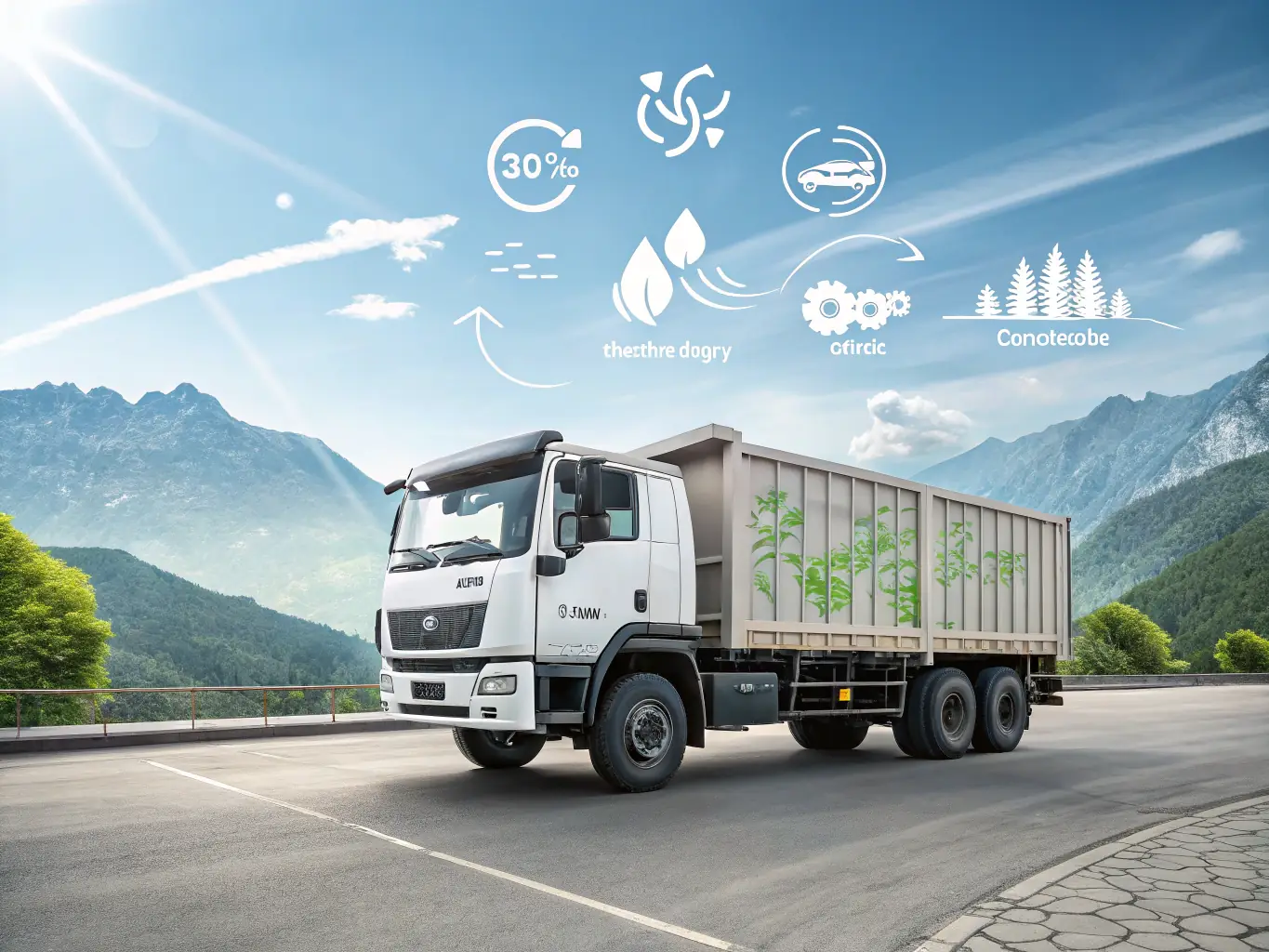
Significant Cost Savings
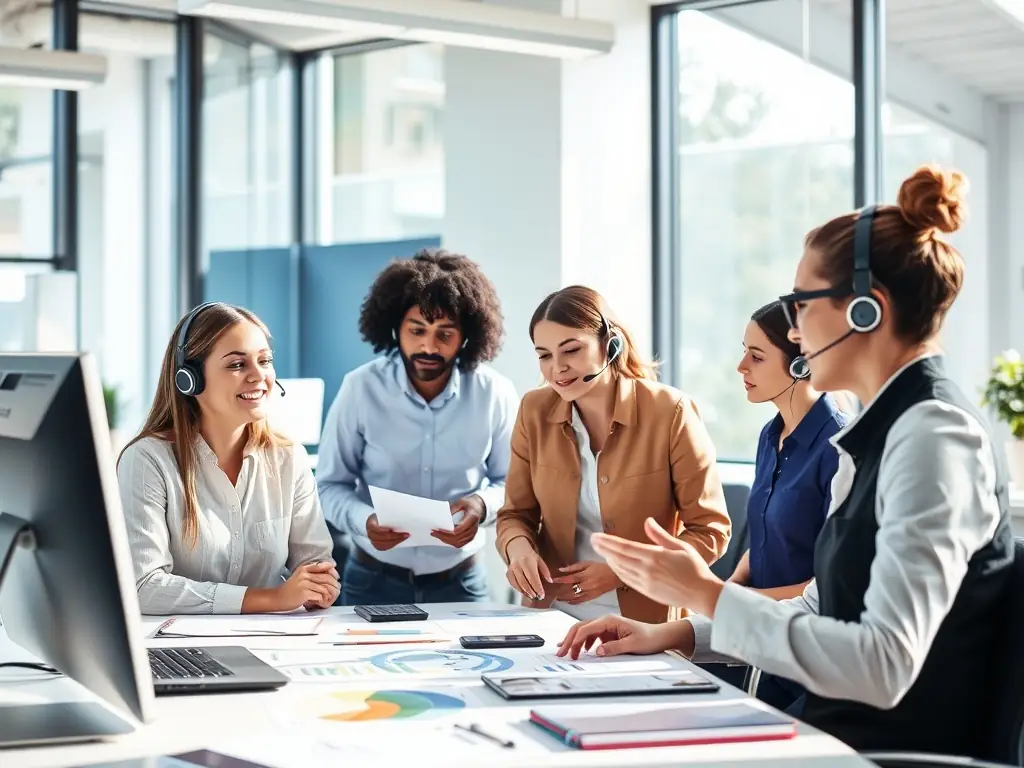